UV硬化科学
硬化とは、重合プロセス中に発生する化学反応を指します。重合プロセスでは、切断された分子と短いポリマー鎖を結合または架橋して、はるかに長く、硬く、剛性の高いポリマー鎖を形成します。多くの物質はポリマー構造を持っていますが、ポリマー化学とポリマー工学は主にプラスチックとゴムを含む材料とプロセスに焦点を当てています。
ここで使用されている用語について質問がある場合は、UV 硬化用語の記事にアクセスして詳細を確認してください。
UV 光重合は、放射線硬化または単に UV 硬化とも呼ばれ、紫外線エネルギーがインク、コーティング、接着剤、押し出し成形品などの UV 配合材料内で架橋を促進する特定の重合カテゴリです。この技術は、さまざまな業界にわたるさまざまな製造プロセスで、ほぼ 75 年間にわたって効果的に利用されてきました。これは、UV 硬化が高速で設置面積の小さい設備で非常に望ましい材料特性を生み出し、触ると濡れている材料を触ると乾いた固体構造に瞬時に効率的に変換するためです。
多くの用途では、UV 配合は、液体キャリアを含まない固体または高固体材料のみで作られています。固体粒子は、液体であるかのようにさまざまな表面に塗布できるほど小さく、数も十分です。ユーザーや業界のサプライヤーは、UV 硬化の急速な構造変化を乾燥と表現することがありますが、UV 配合インク、コーティング、接着剤は乾燥していません。硬化しています。
対照的に、従来の水性および溶剤系配合物には、実際の液体キャリアが組み込まれており、その主な目的は、さまざまな印刷、スプレー、コーティング、およびディスペンシング方法を通じて、目的の表面に所望の固形分を塗布しやすくすることです。塗布するとキャリアの役割は終了し、強制空気乾燥機または熱乾燥機を使用して蒸発または乾燥する必要があります。蒸発後、部品、基板、または構造の表面に残るのは固形粒子だけです。溶剤キャリアの場合、規制により、蒸発した溶剤を環境に放出する前にアフターバーナーで燃焼させることが求められることがよくあります。
硬化に UV 光を使用しない多くの水性および溶剤系プロセスでは、蒸発を積極的に促進するために、長い乾燥トンネルとエネルギーを消費するオーブンを生産ラインに統合する必要があります。UV 硬化とは異なり、乾燥プロセスでは化学反応の分子変化は起こりません。単に分離した残留固形物が残り、プラスチックや金属などの非多孔質材料の表面に直接付着するか、木材や紙などの多孔質構造にわずかに吸収されます。残留固形物は、引っかき傷、傷、擦り傷、化学分解、風化の影響を受けやすいことがよくあります。多くの場合、水性および溶剤系材料には、透明なトップ コーティングやフィルム ラミネーションなどの他の保護メカニズムを使用する必要があります。
UV 硬化により、長いポリマー鎖と非常に強力な分子構造が、非常に望ましい物理的、機械的、および美的に美しい特性をもたらし、最終的には数多くの日常品の全体的な外観、品質、および性能を向上させます。その結果、UV 硬化は、鮮やかなインクの色、視覚的、触覚的、および触覚的特殊効果、非常に強力な破壊結合、優れた耐薬品性と耐候性、硬度、滑り性、耐衝撃性などの望ましい表面品質を生み出すために、製造業者によって広く使用されています。UV 硬化は、エネルギーを消費するオーブンや乾燥トンネル、揮発性有機化合物 (VOC)、および有害大気汚染物質 (HAP) を排除する点で環境に優しいです。UV 硬化プロセスは、ほんの一瞬で化学架橋を伝播し、反応は終了時に完了するため、最終的な UV 硬化ステーションの直後に、硬化後処理、変換、梱包、組み立て、充填、および出荷がすべて可能です。
光科学
電磁スペクトルは、地球上の物体や天体から放射される光を含む、宇宙のすべての光の連続範囲を表します。光は常に放射源から外側に放射されるため、電磁放射または単に放射と呼ばれることがよくあります。次の図は、電磁スペクトルのグラフィック表現を示しています。
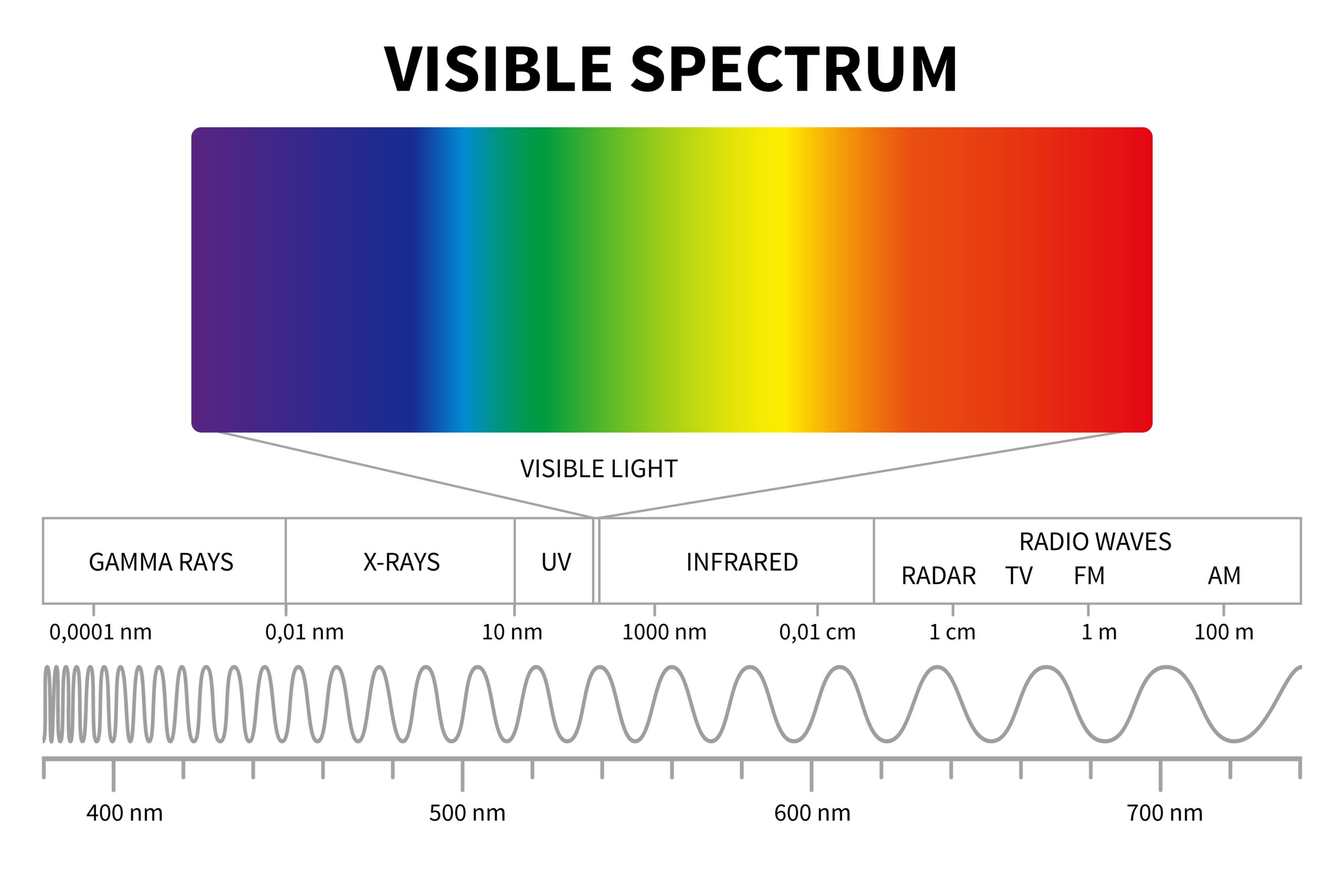
電磁スペクトルは、ガンマ線、X 線、紫外線、可視光線、赤外線、電波に分割されています。紫外線帯域はさらに、真空紫外線、UVC、UVB、UVA、UVV に分割されています。電波はレーダー、テレビ、FM、AM に細分化され、マイクロ波はレーダーのより小さなサブセグメントとして、より一般的には赤外線と電波の間の明確な帯域として区別されます。スペクトルの各スライスは、波長、周波数、および光子エネルギーによって個別に定量化されます。物体と相互作用すると色を生成する可視光線を除き、スペクトル内のすべての光は目に見えません。
光の帯域間の境界は厳密ではなく、一方の波長が終了し、他方の波長が始まる波長は公式に定められていません。そのため、業界、組織、規格、測定機器によって参照する範囲は若干異なります。UV 硬化の目的では、一般的に次の範囲が使用されます。
- 真空 UV (100 – 200 nm) – 100 ~ 200 nm の電磁スペクトル部分。真空 UV 波長は、真空中で最もよく伝わり、空気中を伝わらないため、このように呼ばれています。硬化システムから放出される真空 UV は、UV システムと硬化表面が窒素不活性環境で動作している場合にのみ、光重合プロセスで有効です。不活性環境の酸素濃度によっては、真空 UV がオゾンを生成する可能性があります。
- UVC (200 – 280 nm) – 200 ~ 280 nm の電磁スペクトル部分。UVC は一般に短波長 UV または殺菌 UV と呼ばれ、人間の目には見えません。オゾンは通常、240 nm 以下の UVC 波長で生成されます。UVC 波長は UV 化学反応の表面で吸収され、表面硬化を促進します。
- UVB (280 – 315 nm) – 280 ~ 315 nm の電磁スペクトル部分。 UVB は人間の目には見えません。UVB の波長は UVC よりも化学の奥深くまで浸透しますが、UVA や UVV ほど深く浸透することはありません。
- UVA (315 – 400 nm) – 315 ~ 400 nm の電磁スペクトル部分。UVA は UV エネルギーの最大部分を占め、一般に長波長 UV と呼ばれます。UVA は人間の目が色として認識できる範囲の下限です。UVA の波長は UV 化学の奥深くまで浸透します。
- UVV (400 – 450 nm) – 電磁スペクトルの 400 ~ 450 nm の部分。V は可視を表します。これらの波長は人間の目には色として認識され、可視スペクトルの小さな部分に重なるためです。UVV 波長は UV 化学に深く浸透します。
- 紫外線 (100 – 450 nm) – 電磁スペクトルの 100 ~ 450 nm の部分。UV 波長と可視波長の境界は正確に定義されておらず、一般的に 400 ~ 450 nm の間にあると考えられています。UV 波長は、人間の目に紫色として見える波長のすぐ外側にあります。
- 可視 (400 – 700 nm) – 電磁スペクトルの 400 ~ 700 nm の部分。可視光にはすべての色合いが含まれており、物体に反射する異なる波長または波長の組み合わせによってさまざまな色が生成されます。可視スペクトルは、多くの場合、虹で表されます。
- 赤外線 (700 nm – 0.1 mm) – 700 nm から 0.1 mm の間の電磁スペクトルの部分。赤外線波長は、人間の目が赤として見る波長のすぐ外側にあります。赤外線波長には、熱を発するものと発しないものがあります。赤外線波長は、電極式およびマイクロ波式 UV 硬化システムから放射される熱の主な要因です。比較的単色の UV LED 硬化システムは赤外線を発しません。
- マイクロ波 (0.1 mm – 10 cm) – レーダーの端に位置する 0.1 mm から 10 cm の間の狭い帯域で、電磁スペクトルのはるかに広い電波部分です。マイクロ波は、無電極式またはマイクロ波硬化システムで使用される特定のタイプの UV 硬化ランプに電力を供給するために利用できます。
マイクロ波や電極アークランプなどの従来の広帯域 UV 光源は、UVA、UVB、UVC、UVV に加えて可視光線と赤外線を放射しますが、市販の LED 硬化光源は、可視光線に近い比較的狭い帯域の UVA (365、385、395、405 nm) を放射します。その結果、従来配合された広帯域 UV 化学物質は、一般的に UV LED では十分に硬化せず、より長い UVA および UVV 波長のみで硬化するように再配合する必要があります。幸いなことに、インク、コーティング、接着剤の企業は、単一の配合で LED ランプと従来のランプの両方で硬化できるように UV LED 化学物質を設計する傾向が高まっています。今後数年間で、ますます多くの配合がこの二重硬化機能に移行し、業界の UV LED 硬化への徐々にではあるが避けられない移行を促進するでしょう。
波長、周波数、光子エネルギー
電磁スペクトルの各スライスは、波長、周波数、および光子エネルギーによって個別に定量化されます。波長は、周期的な光の波上の対応する点間の距離の測定値です。通常はギリシャ文字のラムダ () で表されます。周波数は、特定の波長が発生する速度です。これは、1 秒あたりのサイクル数またはヘルツ (Hz) で測定され、通常は文字 (f) または (v) で表されます。周波数と波長は光速によって関連付けられており、周波数は光速を波長で割ったものです。波長が長くなると、周波数は低下します。逆に、波長が短くなると、周波数は増加します。
周波数と波長の両方を使用して、スペクトル内のすべての電磁放射のエネルギーを計算できます。これは、プランク-アインシュタインの関係として知られる次の 2 つの同等の式のいずれかを使用して実行されます。
ここで:
E = 光子エネルギー (ジュール)
h = プランク定数 (ジュール·秒)
c = 光速 (メートル/秒)
λ = 波長 (メートル)
v = 周波数 (サイクル/秒)
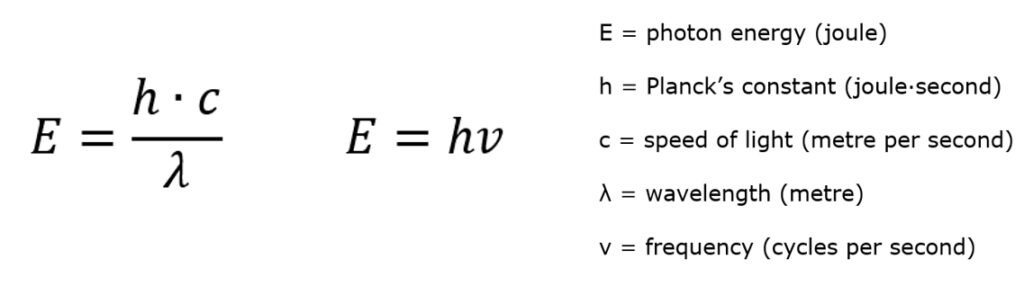
プランク-アインシュタインの関係によれば、UVC などの短い波長は、UVA などの長い波長よりもエネルギーが高くなります。さらに、紫外線帯域のすべての波長は、可視光線、赤外線、マイクロ波、電波よりもかなりエネルギーが高く、X 線やガンマ線よりもエネルギーが低くなります。
放射照度(W/cm2)
放射照度は、単位面積あたりの表面に到達する放射パワーです。ワットまたはミリワット/平方センチメートル (W/cm2 または mW/cm2) で表されます。放射照度の一般的な用語には、電力密度やワット密度などがあります。技術的には正しくありませんが、放射照度は一般的に強度と呼ばれており、強度が使用される場合は、一般的に放射照度を意味すると理解されています。放射照度は通常、広範囲の紫外線波長にわたる最高ピーク値として、または UVC、UVB、UVA、UVV のより狭いセグメント内のピーク値として測定および報告されます。放射照度は、測定に使用する放射計と、UV 光源に対する放射計の位置を常に参照する必要があります。
硬化表面と UV 硬化システム間の定義された距離では、放射照度はランプ電力設定ごとに固定されており、生産ラインの速度や露出時間には依存しません。つまり、硬化表面での放射照度はランプ電力の増加とともに増加し、ランプ電力の減少とともに減少します。ランプ電力設定と距離が変わらない限り、硬化表面での放射照度の値はライン速度に関係なく一定のままです。
フラットガラス UV LED 硬化システムおよびフラッド プロファイルを備えた水銀灯の場合、放射照度は硬化面の各ポイントとランプヘッド間の距離によって影響を受けます。どちらの場合も、距離が長いほど硬化面の放射照度は低くなります。これは、放射された光線が発光源から遠ざかるにつれて互いに拡散または発散するためです。これにより光の集中度が低下し、放射照度が低下します。集束型水銀灯の場合、放射照度は焦点距離で最大になり、硬化面が焦点距離の内側または外側に移動すると減少します。集束型水銀灯の目的は、放射された UV エネルギーのほとんどを狭い帯域に集中させて、放射照度の絶対値を増やすことです。
製造現場では、ほとんどの硬化面が動的放射照度にさらされます。動的放射照度は、ランプヘッドが停止せずに硬化面上を通過するとき、または硬化面が停止せずにランプヘッドの下を通過するときに発生します。硬化面上の点の位置が UV 源に近づいたり、反対に向いたり、遠ざかったりすると、各位置および各瞬間に入射する対応するピーク放射照度は変化します。
動的照度プロファイルはさまざまな形状をとることができますが、一般的には、次の図に示すベル曲線として存在します。グラフでは、照度プロファイル上の各ポイントは、各時点でのピーク照度を捉えており、ベル曲線の頂点は、硬化表面が水銀灯の焦点領域または UV LED ランプの中心を通過する瞬間を示しています。ピーク照度が大きい光源は、プロファイル ピークが高くなります。ピーク照度が低い光源は、プロファイル ピークが短くなります。プロファイルの幅は、UV ランプヘッドの幅と、プロセス ライン速度または露出時間によって決まります。
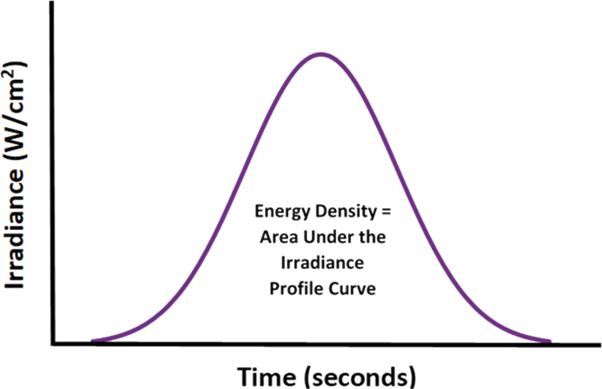
エネルギー密度 (J/cm2)
エネルギー密度は、単位面積あたりの表面に到達する放射エネルギーの総量であり、J/cm2 または mJ/cm2 で表されます。エネルギー密度は、照射時間に対する放射照度 (W/cm2 または mW/cm2) の積分です。これは、前の画像に示すように、放射照度プロファイルの下の面積で表されます。照射時間、つまりエネルギー密度または曲線の下の面積は、ライン速度を遅くしたり、滞留時間を長くしたり、硬化源を追加したり、UV LED の場合はヘッドの幅を広くしたりすることで増加します。図で表すと、これらのアクションにより、ベル型曲線の幅がより長い期間に広がったり、ピークが平坦になったり、複数のランプヘッドを直列に使用すると複数の明確なピークが生じたりします。
特定の硬化アプリケーションでは、正しいスペクトル出力と最小しきい値放射照度が硬化表面に供給されると、硬化速度と硬化度に影響を与える最も重要な要因はエネルギー密度です。放射照度はエネルギー伝達または電力の速度ですが、エネルギー密度は供給される総エネルギーです。より高いエネルギー密度を提供する UV 硬化源は、より低いエネルギー密度の硬化システムよりも速いライン速度で硬化を可能にします。
技術的には正しくありませんが、エネルギー密度は一般に線量と呼ばれ、線量が使用されるときは常にエネルギー密度を意味すると理解されています。明確にするために、エネルギー密度は送達されたエネルギーであり、線量は吸収されたエネルギーです。吸収されたエネルギーを実際に定量化することは非常に困難ですが、エネルギー密度は UV 放射計とエネルギー密度テストストリップを使用して概算できます。放射計で取得したエネルギー密度値を報告するときは、常にメーターとライン速度に注意することが重要です。
硬化化学と光重合
UV 硬化の化学反応は、特別に配合されたインク、コーティング、接着剤、および押し出し成形品内に分散された光開始剤に依存します。光開始剤は 100 ~ 450 nm の波長の光にさらされると、UV エネルギーを吸収し、フリーラジカルまたはカチオン種を生成します。励起された種は、開始、伝播、および終結を通じて反応を促進し、原材料成分の分子構造を急速に変化させます。UV 硬化アプリケーションでは、主にフリーラジカル硬化メカニズムが使用され、カチオンアプリケーションはすべての UV 硬化化学のうちわずか数パーセントを占めるだけです。
フリーラジカル硬化により、架橋反応を促進するフリーラジカルが生成されます。フリーラジカル硬化を開始および伝播するには、連続的かつ直接的な視線 UV 照射が必要です。反応はほんの一瞬ですぐに終了し、望ましい特性を持つ新しい材料形態が得られます。フリーラジカル化学は、特に硬化表面で酸素の影響を受けやすくなります。酸素分子は、硬化プロセスからフリーラジカルを奪い、フリーラジカルの強度を低下させます。ランプの照射量を増やしたり、窒素環境で硬化させたり、化学変化を起こしたりすることが、酸素阻害に対抗するために広く使われている手段です。
代替の、あまり使用されていない硬化メカニズムは、カチオン硬化です。この反応により、架橋を促進するカチオンが生成されます。カチオン硬化では、硬化を開始するために UV 照射が必要ですが、連続的または完全な直接視線 UV 照射なしでも伝播が進行します。化学と用途に応じて、カチオン硬化プロセスは、完全に終了するまでに数分、数時間、または数日かけて伝播します。カチオン化学は、架橋を妨げる可能性のある湿気と温度に敏感です。そのため、カチオン化学を使用する場合は常に、周囲の環境条件を監視し、制御する必要があります。
フリーラジカルであれカチオンであれ、UV 硬化性配合物は、市販の材料から配合されます。選択肢はかなり多様ですが、ほとんどの原材料は次のタイプに分類されます
- 光開始剤 – 特定の波長範囲にわたって紫外線エネルギーを吸収し、フリーラジカルまたはカチオンの生成を通じて光重合反応を引き起こす分子。光開始剤は、総 UV 配合物の重量の 0.5 ~ 15% を占めます。
- モノマー – 比較的分子量が低く、構造が単純な樹脂分子の一種で、それ自体または他の類似の分子と結合して UV 架橋ポリマーを形成できます。モノマーは、全体的な粘度を調整し、硬化した材料の特性に影響を与えるために使用される反応性希釈剤です。モノマーは、配合物の総重量の最大 50% を占めることができ、まれに、一部または全部が水または溶剤に置き換えられることがあります。
- オリゴマー – 比較的分子量が低く、構造が単純な樹脂分子の一種で、それ自体または他の類似の分子と結合して UV 架橋ポリマーを形成できます。オリゴマーは架橋材料のバックボーンを構築し、硬化した材料の特性の多くに影響を与え、配合物の重量の 50 ~ 80% を構成します。
- 添加剤 – 硬化前の混合物の特性と硬化後のポリマーの特性を微調整するために追加されるその他のすべての成分。添加剤には、流動性調整剤、消泡剤、分散剤、光安定剤などが含まれます。添加剤は、顔料とともに、UV 混合物全体の中で最小の割合を占めます。
- 顔料 – 配合物に色を付ける特定の種類の添加剤。
化学者は、光開始剤、モノマー、オリゴマー、添加剤、そして時には顔料を混合して、UV 硬化インク、コーティング、接着剤、および押し出し成形品を作ります。最適な UV 波長 (nm) と放射照度 (W/cm2) の組み合わせにさらされると、化学反応によってフリーラジカルまたはカチオン種が生成されます。光重合は非常に速く起こり、処理時間は数分の 1 秒です。正確な時間と混合物の適切な架橋能力は、原材料の混合、発光源のスペクトル出力 (nm)、放射照度 (W/cm2)、およびエネルギー密度 (J/cm2)、用途、生産ラインの設定、およびフリーラジカルまたはカチオン硬化メカニズムの使用によって異なります。次の図は、未硬化の UV 配合物と、配合物を適切な UV エネルギー源にさらしたときに生じる架橋を示しています。
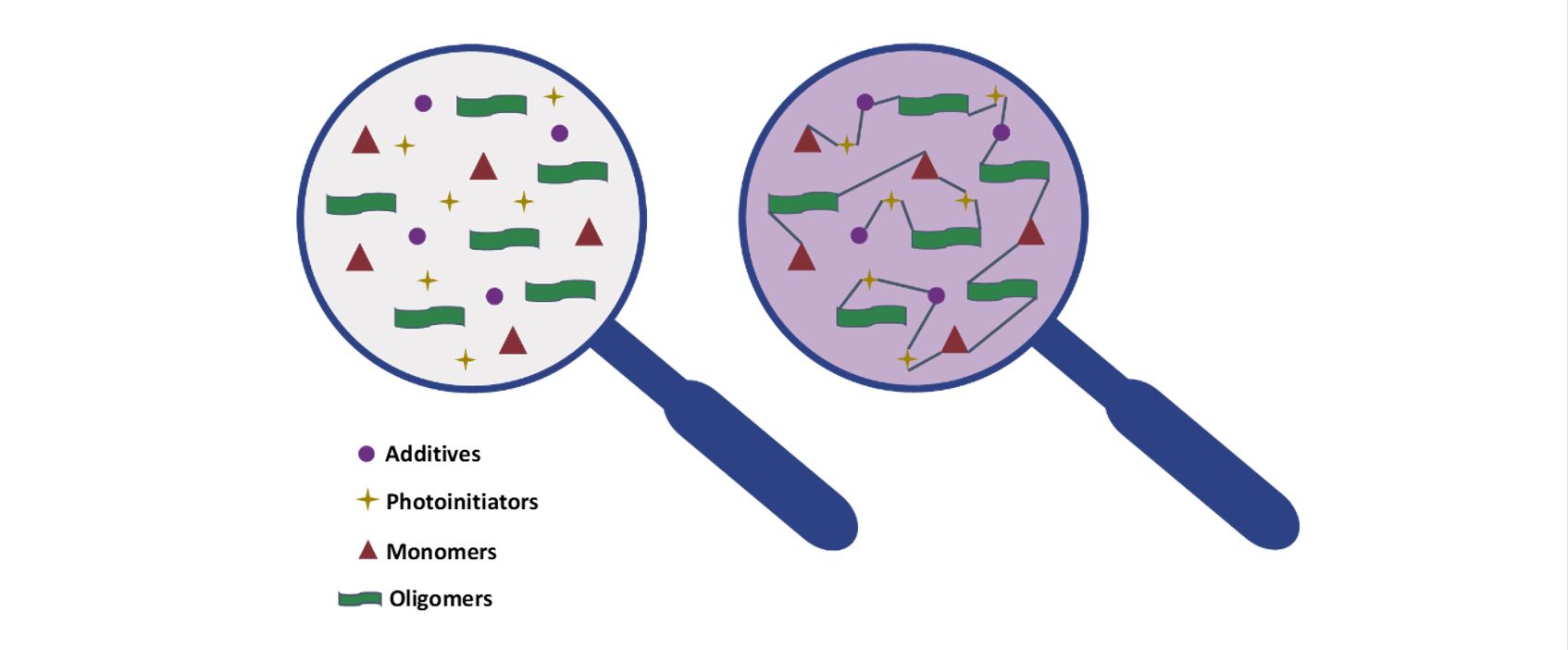
UV 配合物は液体のような性質を持っているため、材料をさまざまな表面や材料に押し出すだけでなく、スプレー、噴射、分配、ロール、浸漬、印刷、スパッタリング、吸引、または浸漬することもできます。塗布したら、紫外線エネルギーにさらすだけで、分子を効率的かつ効果的に結合して固体の均質構造にする伝播および架橋反応を誘発できます。
硬化までの工程
UV 硬化中に発生する架橋反応は、硬化前と硬化後に発生する一連の多くの相互に関連する製造プロセスのうちの 1 つのステップにすぎません。品質と最終用途の性能要件の両方を満たす製品を一貫して生産するには、すべてのステップを特定し、プロセスに組み入れ、相互の影響を評価し、維持する必要があります。
UV 硬化に関連するプロセス ステップには、多くの場合、次のものが含まれます。
- 硬化表面の評価 – 硬化表面の形状、構造、材料の種類、材料の品質、表面エネルギー、および清浄度が重要です。これらの側面によって、前処理が必要かどうか、適切なインク、コーティング、または接着剤の配合、材料の取り扱い、および UV ランプヘッドの必要な向きが決まります。表面はプロセス開発中に評価し、通常の生産中に定期的に評価する必要があります。
- 前処理と基板の変更 – 部品および材料の表面は、多くの場合、洗浄、静電気の除去、または表面エネルギーを高めるための処理が必要です。これらの手順は、インク、コーティング、および接着剤の濡れを促進し、接着性を向上させるために必要となることがよくあります。処理には、洗浄、化学浴またはワイプ、静電気防止装置、プライマー、ベースコート、またはサイジングの適用、炎、コロナ、プラズマ、サンディング、およびグリットブラストなどがあります。
- 材料の取り扱い – 材料表面は通常、シート、ウェブ、または 3 次元部品として生産装置に供給されます。材料の取り扱いでは、インク、コーティング、または接着剤を材料の表面に均一に塗布し、ランプヘッドから定義されたオフセット距離で UV 光源にさらすことができる必要があります。
- インク、コーティング、または接着剤の配合 – 用途、材料表面、配合の供給方法、硬化システムとその UV 出力、ライン速度またはサイクル率、および最終使用要件はすべて、配合に必要な特性を決定します。最適な配合が使用されるようにするには、これらの詳細を配合ベンダーと共有することが重要です。
- 配合供給装置 – インク、コーティング、および接着剤は、製造プロセス中に、スプレー、ジェット、ディスペンス、ロール、ディップ、転写、スパッタ、真空、または浸漬など、さまざまな方法で塗布できます。塗布装置は、配合、硬化する部品の種類、部品の材料、および形状またはプロファイルに適合する必要があります。プロセスライン速度も、必要なエネルギー密度を決定する要因です。
- 液体キャリアの蒸発 – 一部の UV 配合には、紫外線にさらす前に蒸発させる必要がある水または溶媒キャリアも含まれています。場合によっては、部品が硬化源まで移動する時間が蒸発を起こすのに十分な時間であり、また、蒸発を促進するために乾燥メカニズムをプロセスに組み込む必要がある場合もあります。
- UV 硬化 – フリーラジカル化学では、直接の視線での UV 照射、配合物中の光開始剤と一致する UV 波長、硬化表面からのランプの距離に対応する最小閾値放射照度、および所望のライン速度で硬化するのに十分なエネルギー密度が必要です。多くの用途では、塗布されるインク、コーティング、および接着剤ごとに専用の UV 硬化システムが必要です。他の用途では、1 回のランプヘッド照射で複数の配合物を同時に硬化できます。
- 補助プロセス機器 – 多くの UV 硬化用途では、硬化を補助したりプロセス条件を管理したりするために他の機器が必要です。これには、窒素不活性化システム、冷却ローラーまたは冷却プレート、正圧パージまたは加圧ランプヘッドまたは硬化チャンバー、クリーンルーム、外部光学系、UV フィルター、および統合 UV 測定システムが含まれます。
- 硬化後処理 – 部品または材料表面が硬化すると、多くの場合、変換、仕上げ、組み立て、充填、梱包、および出荷が必要になります。
- 品質検査 – 用途ごとに品質と性能の仕様が異なります。場合によっては、これに色合わせが含まれます。また、より機能的な特性が含まれる場合もあります。必要に応じてプロセス変数を修正し、生産中に定期的に監視できる定量化可能なターゲットを提供するプロセスを導入する必要があります。
- 最終使用時の性能 – 最終製品の使用条件は、このリストにあるすべての先行プロセス ステップを決定する上で非常に重要です。最終使用に関して、すべてのプロセス関連ベンダーと話し合うことが重要です。
- 資格、承認、および認証 – 処理され UV 硬化されるアイテムは、最終的に別の当事者に提供されますが、その当事者は、全体的な製造プロセスがニーズや企業目標に適しているかどうかを決定する特定の要件を持っている場合があります。購入側から適切な資格、承認、および認証を取得し、適切な検査ログを維持することは、多くの場合、重要なステップです。
提供されている箇条書きのリストは UV 硬化プロセスの堅実な概要を表していますが、必ずしもすべての可能なアクティビティを完全に網羅したリストではありません。各 UV 硬化アプリケーションと各 UV 製造ラインには固有の特性があり、リストされていないプロセス ステップを導入する可能性があります。いずれにしても、UV 硬化アプリケーション、プロセスが統合される製造ライン、硬化後の処理アクティビティ、および最終製品の使用を、各ステップが他のステップに影響を与える可能性のある完全なプロセスとして評価することが常に重要です。幸いなことに、UV 硬化プロセスが確立されると、それは信じられないほど信頼性が高く、繰り返し可能で、制御可能です。
全体として、UV 硬化により、メーカーは物理的、機械的、および美的に非常に望ましい特性を持つ製品を製造することができ、最終的には多くの日常的なアイテムの全体的な外観、品質、およびパフォーマンスが向上します。UV 硬化、光科学、UV 化学、およびプロセス変数の基礎を理解することで、最適な UV 硬化ソースと処方の選択、適切な統合、プロセス制御、および高品質の製品の一貫した製造が容易になります。